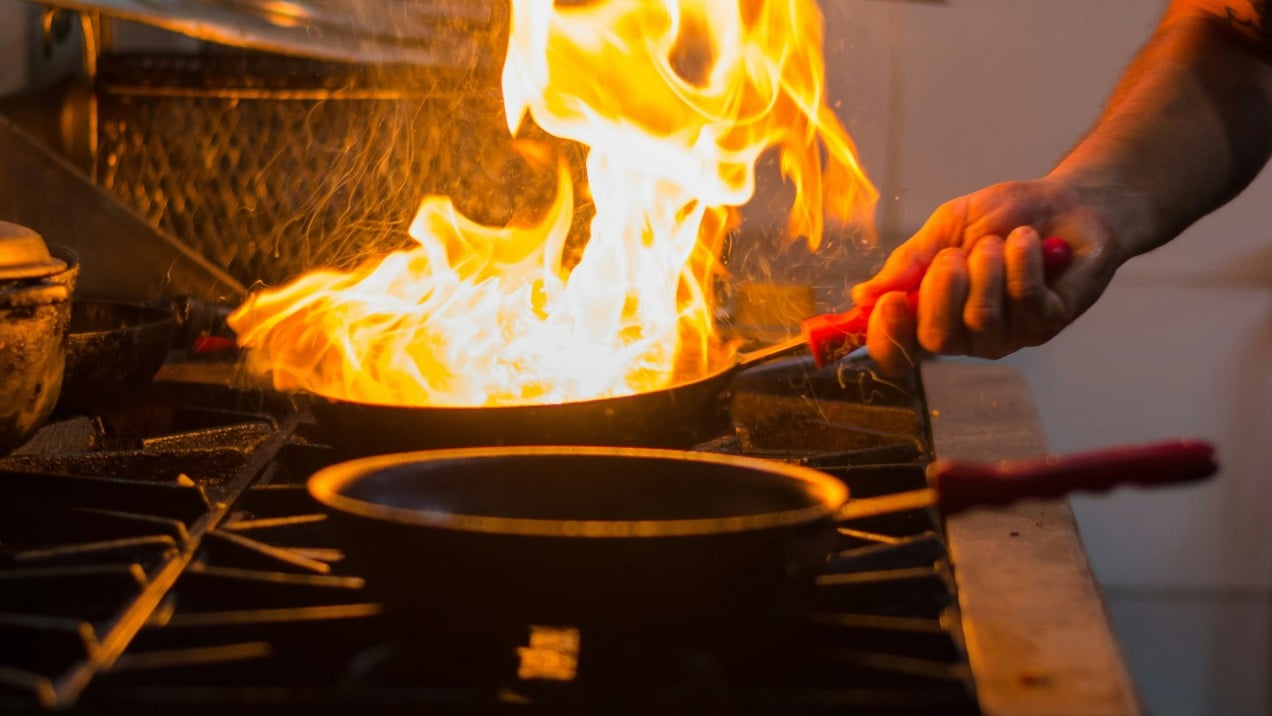
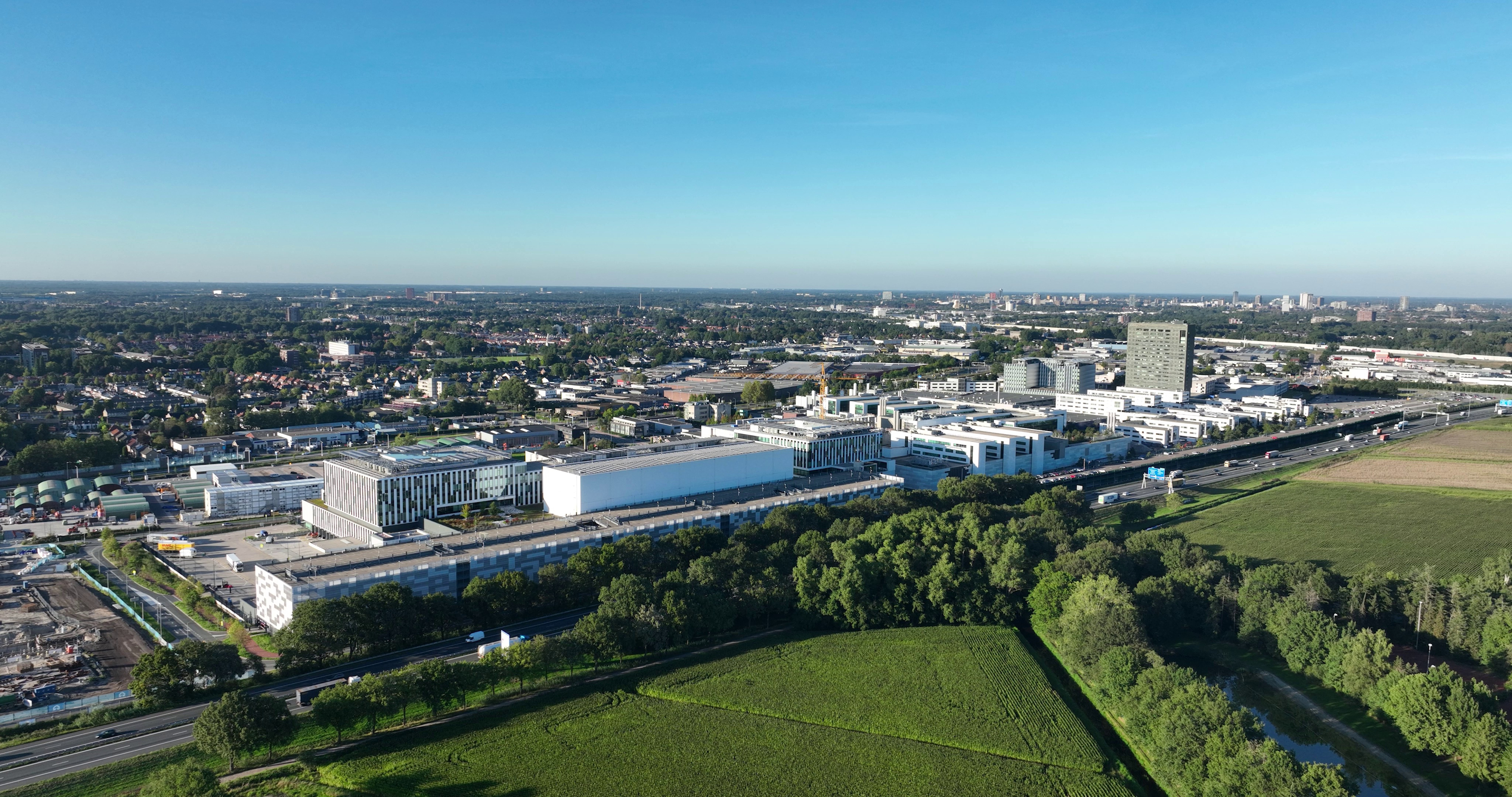
Every business transformation begins with a first step. Implementing technology that touches every part of a business, especially when combining OT with IT, requires building a solid foundation before tackling the bigger pieces.
For this case study we're looking at a U.S.-based consumer goods company that designs and manufactures packaging for globally recognized brands and products, including food, beverage, home and garden, and beauty products.
The manufacturer began its ServiceNow transformation with a key move – building out its OT configuration management database (CMDB) through a full asset inventory.
This was the company's first step in an ongoing partnership with CoreX, bringing ServiceNow's full power to their enterprise operations.
Understanding the need to modernize
The packaging manufacturer’s OT transformation was driven by multiple factors: the need to support SOCS compliance as a publicly traded company, cybersecurity concerns due to limited OT visibility, IT and OT convergence, and overdue equipment upgrades. Implementing ServiceNow OT provided a strategic way to plan and manage these upgrades efficiently.
The challenge was that the company needed to modernize its operational processes.
Going into specific issues, the client was looking to solve the challenge of manual asset tracking and reliability incident logging. Before implementing ServiceNow OT, the manufacturer relied on Excel for device lists and managed OT incidents and changes through legacy homegrown applications. The goal was to standardize its OT in ServiceNow and adopt IT best practices with a drive toward a unified OT Service Desk.
Another concern driving the manufacturer to an OT transformation was that the company had expanded its manufacturing footprint from paper mills to board manufacturing, along with growth through acquisition. This meant different parts of the company were siloed with no full-scale integration to establish baseline day-to-day operating standards.
To begin this modernization, the client understood the process needed to happen in stages and phase one would be setting the foundation for the larger enterprise-wide transformation to come.
Laying the OT transformation foundation
To implement its ServiceNow OT transformation, the company partnered with CoreX. Phase one of the partnership was bringing a full asset inventory into ServiceNow using OT. This process began with a month of planning and data review sessions to uncover all the data requirements, how the team was going to get that data, and a manual capture of OT devices.
By taking a hands-on approach, the U.S. based manufacturer quickly populated its OT CMDB. According to Dean Stavrou, Global Head of Industrials Engineering, CoreX, this manual process helped speed the deployment while CoreX guided what they needed to capture out of over 100 OT CMDB device attributes such as name, IP address, and subnet. Paring the asset attributes to capture down to a handful of fields helped streamline the inventory process.
The result of this inventory meant the client was able to populate the OT CMDB and industrial process manager with its devices, capture its manufacturing processes and model those processes in ServiceNow as a digital twin, and finally associate OT devices to the digital twin.
This provided the organization with a full contextual 360 view – a single pane of glass – of each OT device and the manufacturing processes a given device is driving and allowed for real-time asset tracking and visibility. Stavrou said, “It’s all about populating a database to create that solid foundation.”
Gaining visibility is the first step
Phase one of this process was all about the client’s asset inventory visibility and, importantly, getting its devices into ServiceNow. Before the engagement with CoreX, the manufacturer was at around 25-30% device inventory, and by the end of phase one it reached 80% asset inventory in the two plants involved in the effort, a 220% increase.
(We’ll give you a second to digest that.)
The result? Improved visibility simply by understanding what the company had on hand, and it created a foundation for an enterprise-wide expansion with trusted data for better decision-making and downtime planning.
The global packaging manufacturer’s increase in tracking its asset inventory was the tangible outcome of modernizing its OT asset tracking and processes. The key result of phase one was that it allowed the firm to move away from manual efforts and begin automating processes across facilities. Importantly, the solutions CoreX brought to the client were scalable and set the manufacturer up to meet its long-term strategic objectives.
Prepping for the larger business transformation
With the foundation firmly in place, our client is now positioned for enterprise-wide transformation. The phase one asset inventory effort served as the foundation for more dramatic business transformation within the company. The next steps in the partnership with CoreX will involve transforming service management and vulnerability response in areas such as process orchestration and security.
Phase two will be an expansion into service, including automating the discovery process and implementing OT incident, OT chain management, and OT vulnerability response at the two facilities already involved.
With this in place, CoreX will help the company roll the ServiceNow transformation across its enterprise to three additional facilities in 2025. This will allow them to run their business the same way across its functional silos by cutting through technical, skill, and communication gaps.
This case study represents just one part of the larger goal. What began with the OT CMDB has set the stage for modernization across every function at the company’s facilities and across its entire enterprise.